Design Optimization Of Radiator Plastic Tanks For Improved Performance
- linghangtechnology
- Mar 30
- 4 min read
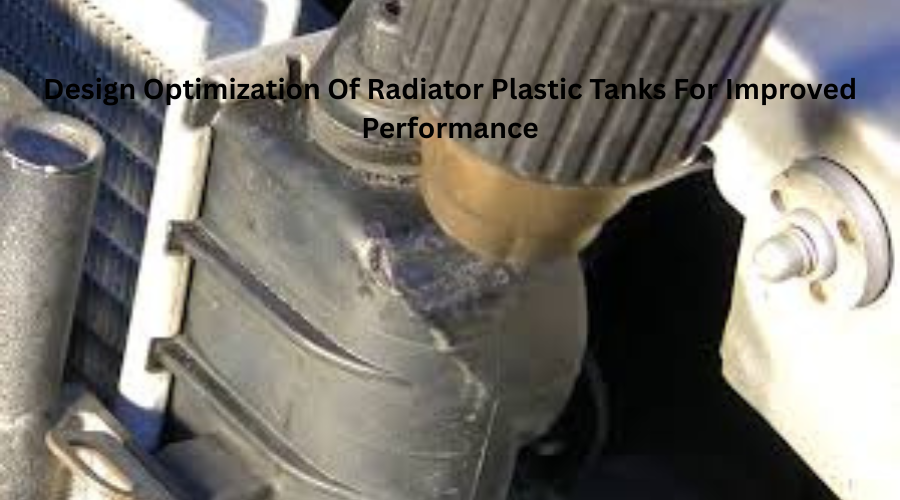
In the automotive industry, radiator plastic tanks play a crucial role in engine cooling systems. These components must be designed to handle high temperatures, pressure fluctuations, and prolonged exposure to coolant fluids. Manufacturers and engineers continuously seek ways to optimize radiator plastic tank design to improve durability, efficiency, and overall vehicle performance. Whether you’re an OEM manufacturer or a supplier dealing with cooling system components, understanding the latest advancements in radiator tank design is essential. If you're looking for Bulk China radiator plastic tank, it’s important to consider key design factors to ensure you get premium products that meet industry standards.
Key Design Considerations for Radiator Plastic Tanks
Optimizing radiator plastic tanks involves several important factors. Each element, from material selection to structural enhancements, plays a significant part in ensuring durability and efficiency. Below are the critical aspects to consider when designing radiator plastic tanks for improved performance:
1. Material Selection
Choosing the right material is the fundamentals of an effective radiator plastic tank design. Engineers typically use high-performance thermoplastics such as glass-reinforced nylon (PA66-GF30) or polypropylene (PP) due to their excellent thermal resistance, mechanical strength, and chemical resistance.
Glass-reinforced nylon offers superior strength and heat tolerance, making it ideal for high-performance applications.
Polypropylene provides a more cost-effective option while still offering good thermal stability.
UV-resistant coatings can be applied to prevent material degradation due to prolonged sun exposure.
2. Wall Thickness and Structural Integrity
The thickness of the plastic tank walls must be optimized to withstand internal pressure while minimizing weight. Thicker walls can improve durability but may add unnecessary weight and cost. Advanced finite element analysis (FEA) techniques help engineers determine the ideal wall thickness for balancing performance and material efficiency.
Stress distribution analysis ensures that the tank can handle extreme temperature variations.
Reinforced ribs in high-stress areas enhance the tank’s mechanical strength.
3. Improved Sealing Mechanisms
A major challenge in radiator plastic tank design is leak prevention. The connection between the plastic tank and the aluminium core must be secure to maintain coolant pressure.
EPDM rubber gaskets are commonly used to ensure a tight seal.
Ultrasonic welding and crimping techniques enhance joint strength and prevent leaks.
High-pressure resistance testing ensures the tank can endure extreme conditions without failure.
4. Optimized Coolant Flow Design
For efficient cooling, the internal flow of coolant within the radiator tank should be optimized. Poor coolant distribution can lead to hot spots, reducing engine performance.
Baffle plates inside the tank help direct coolant flow efficiently.
Reduced turbulence improves heat exchange between coolant and radiator fins.
CFD (Computational Fluid Dynamics) simulations help refine the tank’s internal geometry for maximum cooling efficiency.
5. Enhanced Heat Resistance
Since radiator plastic tanks operate under high temperatures, they must resist thermal expansion and prevent deformation over time.
Heat stabilizers and additives improve material longevity.
Radiator pressure caps regulate pressure fluctuations, reducing stress on the tank walls.
6. Lightweight and Cost-Effective Design
Reducing vehicle weight is a priority in modern automotive manufacturing. Plastic tanks are significantly lighter than traditional metal tanks, improving fuel efficiency and reducing emissions.
Injection molding techniques allow for complex, lightweight designs with high precision.
Automated manufacturing improves consistency and reduces costs in bulk production.
Innovations in Radiator Plastic Tank Technology
Recent technological progress has greatly enhanced the performance of radiator plastic tanks. Some cutting-edge innovations include:
Nano-reinforced polymers, which enhance strength and heat resistance.
Smart sensors integrated into radiator tanks to monitor coolant levels and temperature in real-time.
3D printing technology is used for fast model development and custom designs.
Conclusion
The design optimization of radiator plastic tanks is crucial for enhancing vehicle cooling efficiency, durability, and cost-effectiveness. By focusing on material selection, structural integrity, sealing mechanisms, coolant flow design, heat resistance, and lightweight construction, manufacturers can produce high-performance radiator plastic tanks that meet modern automotive demands. As the industry continues to evolve, advanced materials and innovative manufacturing techniques will further refine radiator tank designs, leading to more efficient and longer-lasting cooling solutions.
FAQs
1. Why are plastic radiator tanks used instead of metal?
Plastic radiator tanks are lighter, cost-effective, and corrosion-resistant compared to metal tanks, making them a preferred choice in modern automotive cooling systems.
2. What materials are best for radiator plastic tanks?
Glass-reinforced nylon (PA66-GF30) and polypropylene (PP) are commonly used due to their excellent heat resistance, mechanical strength, and chemical durability.
3. How do manufacturers prevent radiator plastic tanks from leaking?
Leak prevention is achieved through reinforced sealing mechanisms such as EPDM gaskets, ultrasonic welding, and pressure-resistant designs.
4. Can radiator plastic tanks handle high temperatures?
Yes, high-quality plastic tanks are designed with heat-resistant materials and additives to withstand extreme engine temperatures and pressure fluctuations.
5. What role does coolant flow design play in radiator performance?
Optimized coolant flow design ensures even heat distribution, preventing hot spots and improving overall cooling efficiency.
By considering these factors and innovations, automotive engineers and manufacturers can continue to enhance radiator plastic tank designs for improved performance and longevity.
Comments