How Plastic Radiator Tanks Help Lower Manufacturing Costs?
- linghangtechnology
- Apr 7
- 5 min read
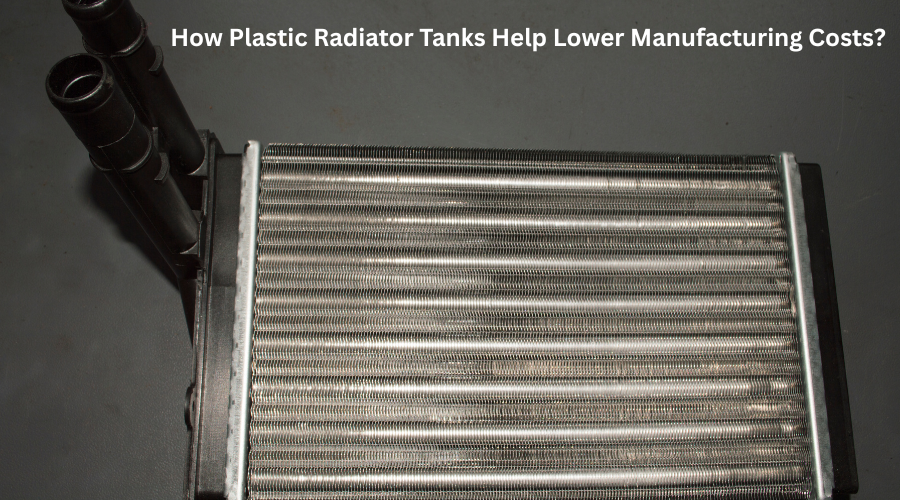
In today's competitive manufacturing landscape, companies are constantly looking for ways to cut expenses without sacrificing product quality. One such innovation that has significantly contributed to cost-saving measures is the use of plastic radiator tanks. As a reliable and cost-effective solution, plastic radiator tanks are gaining momentum in industries ranging from automotive to industrial machinery. In this article, we will explore how these plastic components can help lower manufacturing costs and deliver long-term benefits.
The Rise of Plastic in Radiator Tanks
Traditionally, radiator tanks were made from metals such as aluminum or steel. While these materials were durable, they often came with a high price tag due to the cost of raw materials and the complexity of the manufacturing process. However, with advancements in materials science, plastic radiator tanks have emerged as a viable alternative.
Plastic radiator tanks are now widely used in various applications, from automobile engines to industrial machinery. Many manufacturers, including radiator plastic tank manufacturers, have embraced this innovation because of its inherent advantages in terms of both cost and performance.
Cost Benefits of Plastic Radiator Tanks
So, why are plastic radiator tanks becoming increasingly popular in the manufacturing world? Let's take a closer look at the reasons why these tanks can significantly help reduce costs.
1. Lower Material Costs
One of the most obvious benefits of using plastic for radiator tanks is the lower material cost. Compared to metals like aluminum or copper, plastic is relatively inexpensive to produce. Plastics like polypropylene or polyethylene, which are commonly used for radiator tanks, are readily available and cost-effective. This cost reduction in raw materials translates directly into lower production costs for manufacturers.
2. Lightweight Nature
The lightweight nature of plastic makes it easier to move and manage during the manufacturing process. Metal components, in contrast, can be heavier and require more effort to move or mold into shape. For manufacturers, using plastic radiator tanks reduces the need for special equipment to handle heavy metal parts, cutting down on labor and logistics costs.
Furthermore, the reduced weight of plastic radiator tanks can also be a selling point for industries such as automotive manufacturing. Lighter vehicles tend to consume less fuel, and automakers are always on the lookout for ways to make their products more energy-efficient. By incorporating plastic radiator tanks into their designs, manufacturers can lower their total manufacturing expenses while also offering customers a more fuel-efficient vehicle.

3. Simplified Manufacturing Process
Plastic radiator tanks are easier to mold and shape compared to their metal counterparts. This simplification of the manufacturing process can save manufacturers both time and money. Molding plastic is a faster process than welding or stamping metal, and it requires fewer skilled workers to operate. Additionally, the process of producing plastic radiator tanks generates less waste, as plastic molds can be reused multiple times without compromising quality. This further reduces costs associated with waste management.
4. Lower Energy Consumption During Production
The process of manufacturing metal parts typically involves high temperatures, which means greater energy consumption. On the other hand, plastic production requires lower temperatures, resulting in reduced energy costs. For large-scale manufacturers, this can add up to significant savings. The energy savings from using plastic radiator tanks can make a noticeable difference in overall production costs, particularly for manufacturers operating on a global scale.
5. Corrosion Resistance
Plastic radiator tanks are highly resistant to corrosion and rust, unlike their metal counterparts. Metals, especially aluminum, and steel, are prone to corrosion over time when exposed to moisture and heat, which can lead to expensive maintenance or replacements. Plastic radiator tanks, however, do not suffer from these issues, ensuring extended durability and reducing the need for maintenance. This not only helps manufacturers save money in the long term but also leads to greater customer satisfaction due to the durability of the products.
6. Reduced Maintenance and Repair Costs
The longevity of plastic radiator tanks also means that manufacturers can save on maintenance and repair costs. Plastic tanks are less likely to crack, corrode, or leak compared to metal tanks, making them more reliable over time. This reliability can translate into lower warranty claims and fewer product recalls, further driving down the overall cost of manufacturing.
7. Flexibility in Design
Plastic radiator tanks can be molded into more complex shapes than metal tanks, providing greater design flexibility. This opens up the possibility of creating more innovative and efficient designs that may not be feasible with metal components. The ability to produce tailored shapes and sizes at a lower cost can also help manufacturers differentiate their products in a competitive market.
Environmental Benefits That Lead to Cost Savings
While cost savings are a major factor in the adoption of plastic radiator tanks, there are also environmental benefits that indirectly contribute to lower manufacturing costs. Plastic production has a lower carbon footprint compared to metal production, which involves energy-intensive processes like smelting. Additionally, plastic radiator tanks are fully recyclable, meaning that manufacturers can reuse materials, reducing waste and the cost of sourcing new raw materials.
The environmental aspect is especially important for companies seeking to align with sustainable practices. Governments and consumers alike are placing increasing emphasis on environmental responsibility, and manufacturers who adopt eco-friendly solutions like plastic radiator tanks are better positioned to benefit from these trends. Companies that commit to sustainability are more likely to attract environmentally-conscious consumers, which can lead to increased sales and a stronger market presence.
Conclusion: A Smart Investment for Manufacturers
Plastic radiator tanks are proving to be an excellent solution for manufacturers looking to reduce their production costs without compromising on quality. From lower material and manufacturing costs to energy savings and greater design flexibility, plastic radiator tanks offer a wide array of advantages. These benefits are not only important for manufacturers but also for end-users who will appreciate the improved durability and performance of their products.
As a manufacturer, adopting plastic as a core material for radiator tanks can set your business apart in a highly competitive market. By reducing costs and improving operational efficiency, plastic radiator tanks contribute to both short-term savings and long-term profitability.
By continuing to innovate with materials like plastic, producers can ensure they stay ahead of the competition in an ever-changing industry while meeting the demands for cost-effective and environmentally friendly products.
FAQs
1. What are the most common materials used for radiator plastic tanks?
The most common plastics used for radiator tanks are polypropylene (PP) and polyethylene (PE) due to their durability, heat resistance, and corrosion resistance. These materials are well-suited for the high temperatures and pressures often found in radiator systems.
2. How do plastic radiator tanks compare to metal in terms of heat resistance?
While metals like aluminum and steel have high heat resistance, modern plastics used in radiator tanks are engineered to withstand high temperatures as well. Plastic radiator tanks are designed to handle the heat generated by engines, making them a reliable option for many applications.
3. Can plastic radiator tanks be recycled?
Yes, plastic radiator tanks are recyclable. In fact, recycling plastic is more energy-efficient than recycling metal, contributing to both environmental benefits and cost savings for manufacturers.
4. Do plastic radiator tanks last as long as metal tanks?
Yes, plastic radiator tanks are designed to be highly durable and crack-proof, corrosion, and leaks. In many cases, they offer a longer lifespan than metal tanks due to their resistance to rust and corrosion.
5. Are plastic radiator tanks safer than metal tanks?
Plastic radiator tanks are often safer in terms of impact resistance. They are less likely to deform or rupture upon impact, minimizing the potential for harm or damage to the engine.
By understanding the cost-saving benefits and performance advantages of plastic radiator tanks, manufacturers can make more informed decisions that help them remain at the forefront and sustainable in their operations.
コメント